New Age of Ceramics
Over the past 10,000 years, ceramics have evolved along with technological development. In Japan, the long history of ceramics began with Jomon pottery, and now Brightorb is adding a new chapter to this long history.
Brightorb is a ceramic material for 3D printers developed and manufactured by AGC Ceramics. Brightorb is a ceramic material less than 1% srinkage when firing process. The special material is developed and manufactured by AGC Ceramics.
We support creators and engineers by offering two categories of products: Brightorb Creative, which enables freedom of creativity, and Brightorb Engineering, which enables the production of high-precision casting molds.
More freedom, more precision. The next future begins with ceramics, a material that has walked hand in hand with humanity.
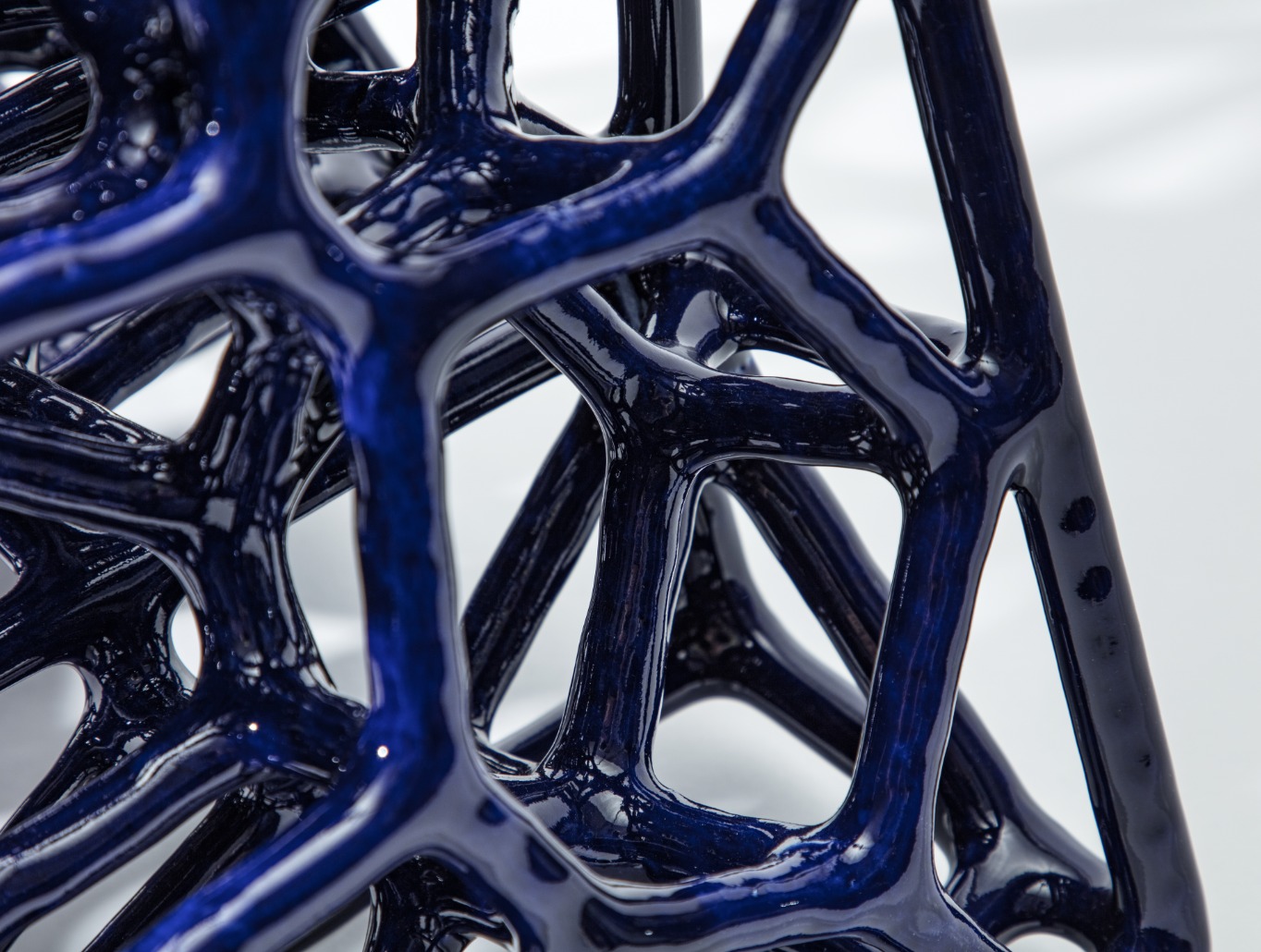
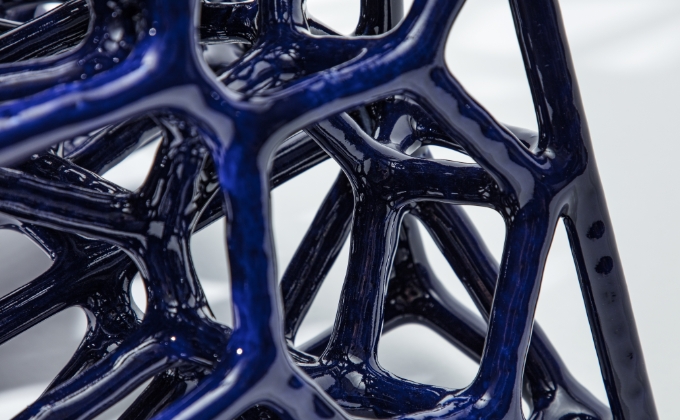
for Unique Expression
It achieves a shape and structure that overturns the conventional standards of ceramics and porcelain. A variety of glazes can be applied to achieve designs with more freedom of expression, not only in color but also in surface texture and uniformity.
3D printing technology controls every detail, while adding the complexity of handwork and nature, and the unique texture of glaze.
The high dimensional accuracy allows for a wide range of combinations with different materials such as glass, wood, and iron. We will go beyond the areas where ceramics have been used for many years, and demonstrate the possibilities in various fields from art, products, crafts, architecture, interior design to fashion.
for Sustainable Molding
Taking advantage of its features such as high fire resistance, high definition, and inorganic materials, the 3D printer produces free molds from a single shape. This eliminates the need for wooden molds or metal molds in the prototyping and development of cast parts, contributing to shorter prototyping and development time and cost reduction.
The main raw material used is artificial sand (FINE-Bz), which is a recycled by-product of the refractory manufacturing process for glass kilns. By using a 3D printer to produce only the molds, we have succeeded in eliminating the need for wooden or metal molds, which were formerly essential in conventional production.
Only the necessary quantity is produced when it is needed. From the molding method, we will realize a sustainable future.
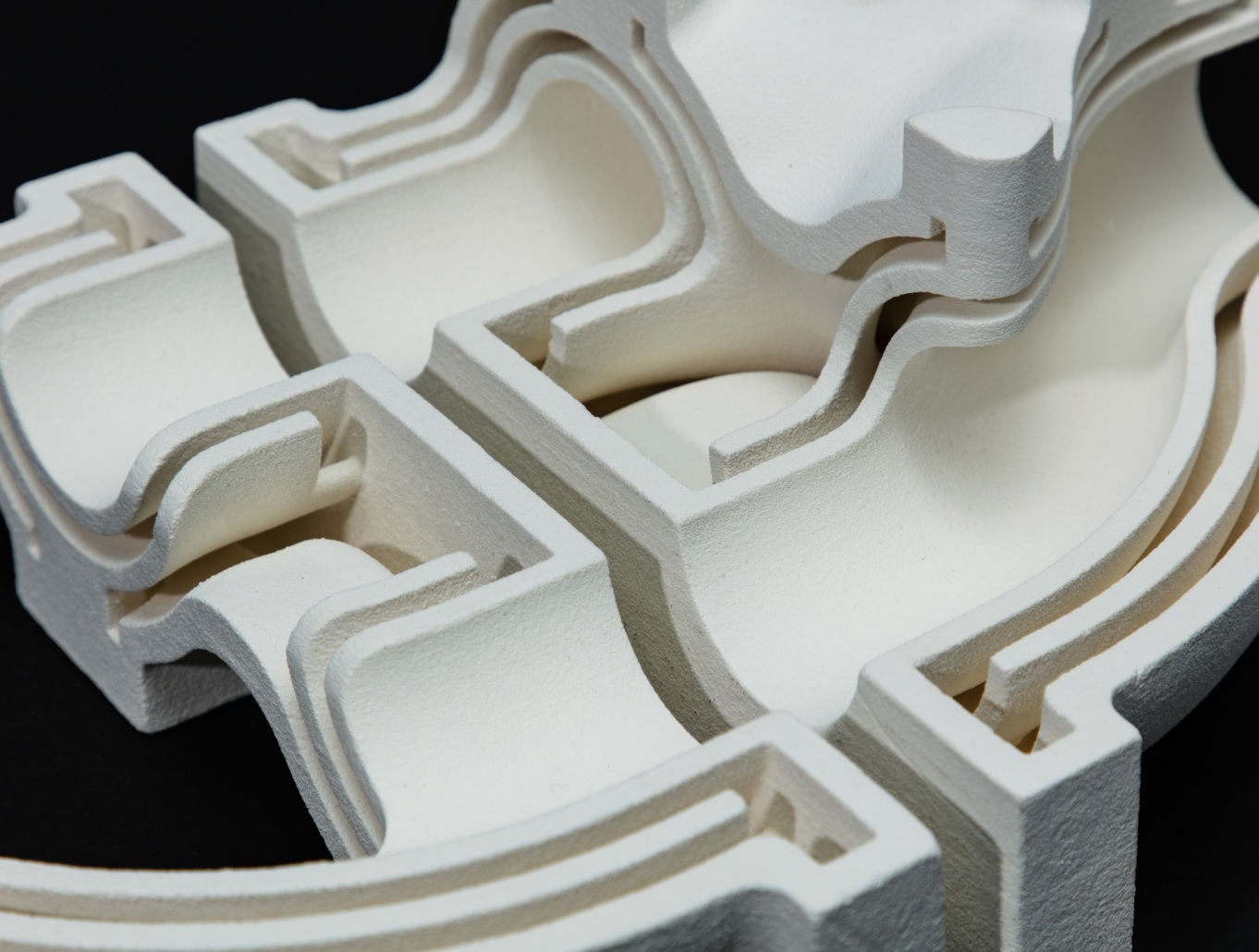

CASE STUDY
Check examples of use
View All project
SPEC
Material Features
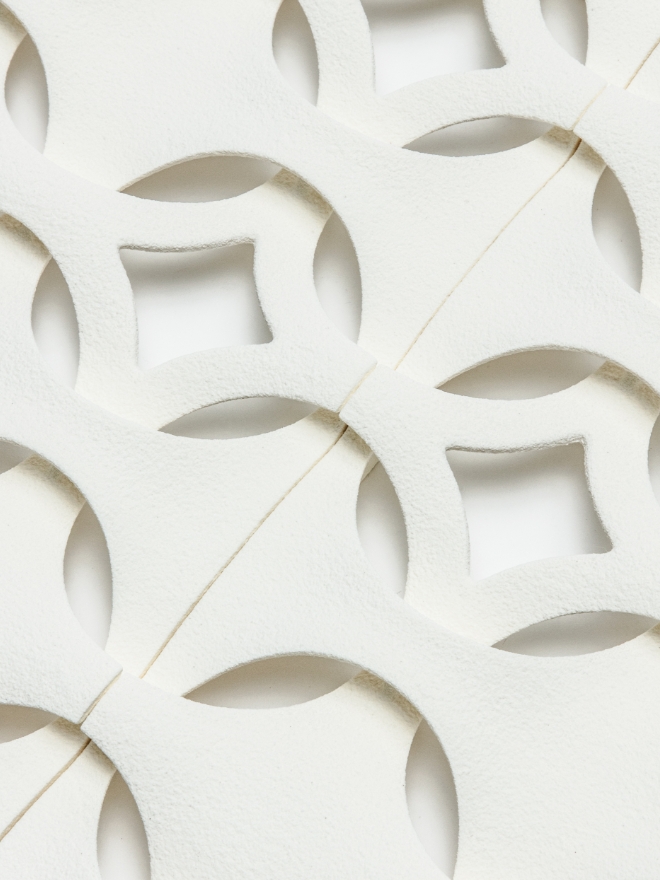
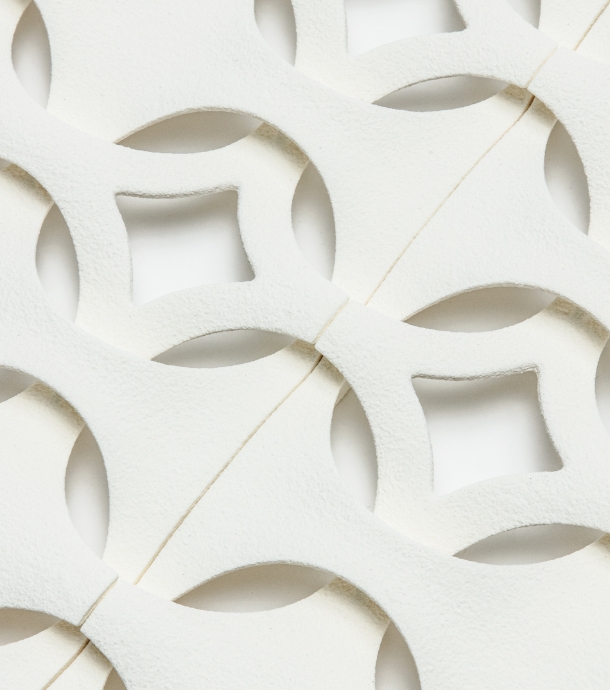
Unique Point01
Ceramics without shrinking and distorting
While conventional ceramic materials suffered from shrinkage and distortion of 10% or more during firing, Brightorb's firing shrinkage rate is approximately 1%. In addition, the high-precision binder-jet 3D printing method achieves high dimensional accuracy. This makes it possible to combine ceramics with other materials, which was difficult in the past.
Unique Point02
Large-scale modeling can be freely designed
Since no support material is needed, the shape can be designed freely, even for large models. The binder-jet 3D printer prints one layer at a time, spraying binder only on the part to be formed, on a layer of powder. In Japan, the maximum size of 900x550x500 mm was achieved without any seams.
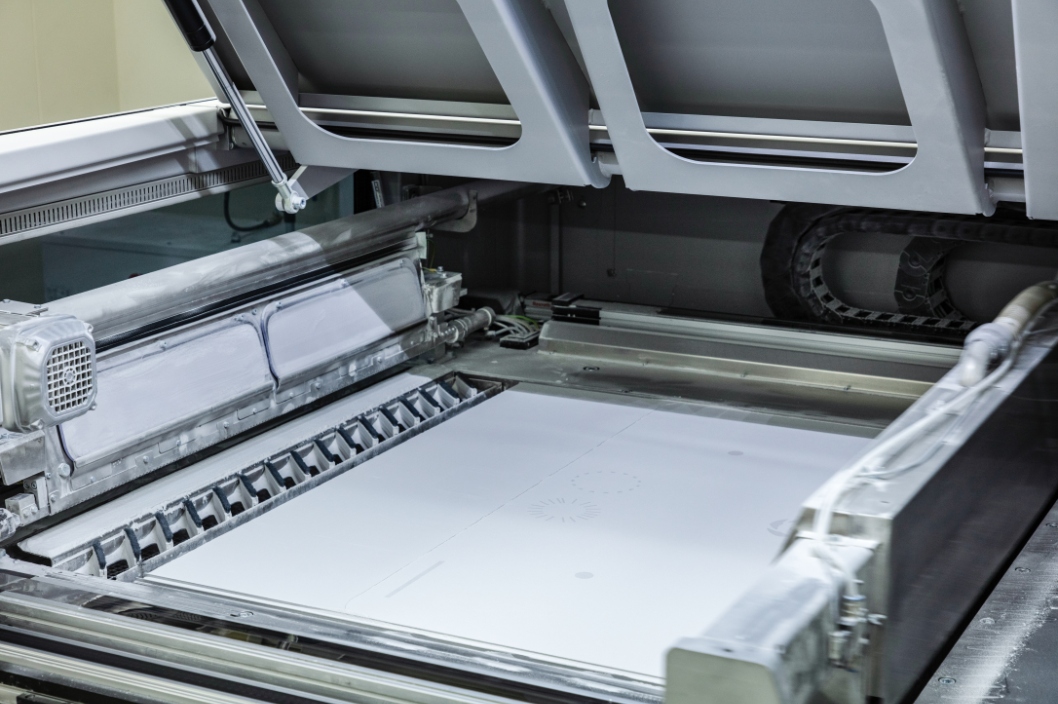
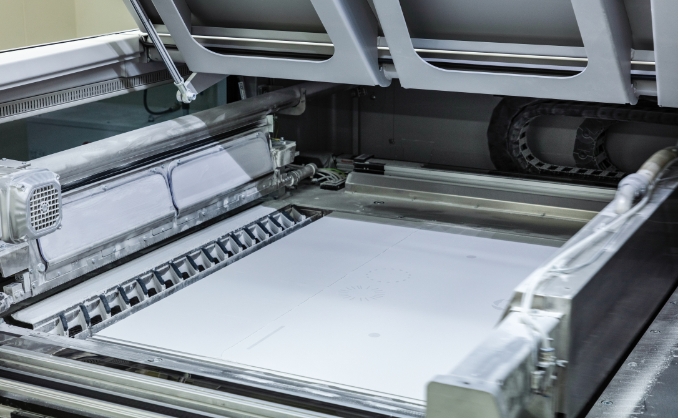
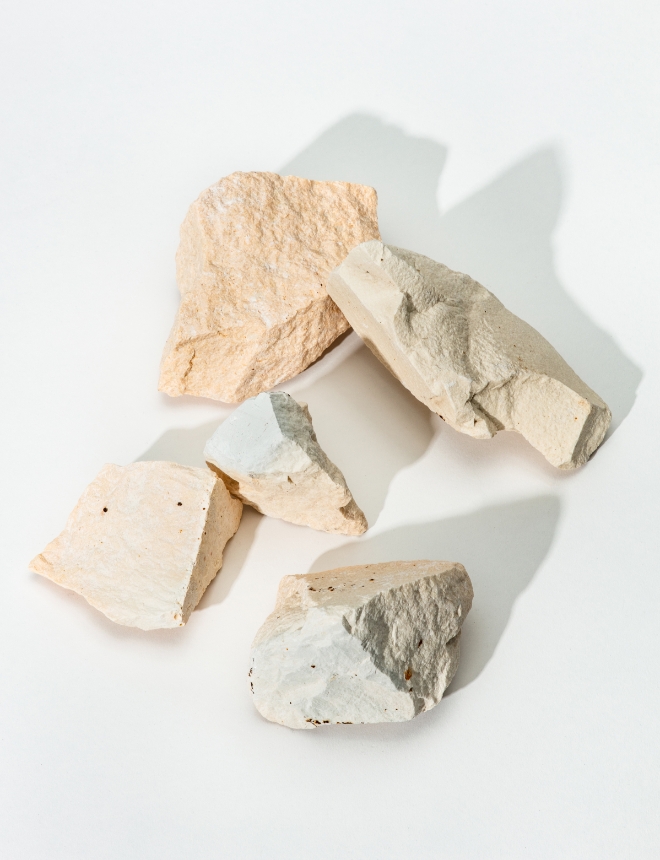
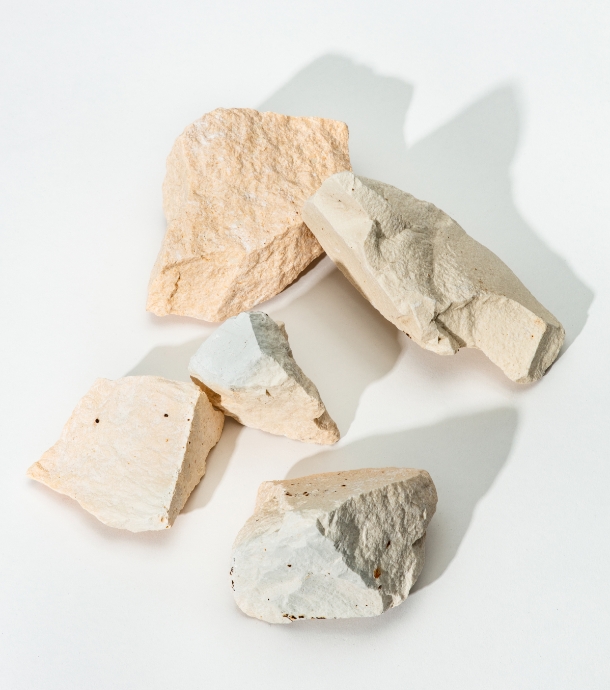
Unique Point03
Sustainable Manufacturing Methods
The main raw material for Brightorb is artificial sand (FINE-Bz), which is a recycled by-product of the refractory manufacturing process for glass kilns. Only the product part is manufactured using a 3D printer machine. In the future, when a 3D printing production base is established near the place of consumption and local production for local consumption becomes possible, transportation energy is expected to be decisevely reduced.
Download spec sheet
PROCESS
CONTACT
AGC Ceramics Co., Ltd.
Additive Manufacturing Office
Mita NN Building Floor 6, 4-1-23,
Shiba, Minato-ku, Tokyo 1080014
Tel +81-3-5442-9191 Fax +81-3-5442-9190
Form